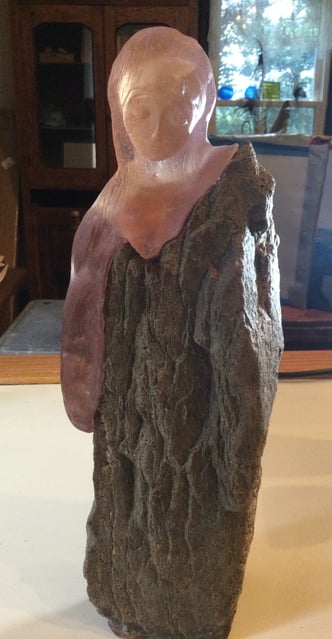
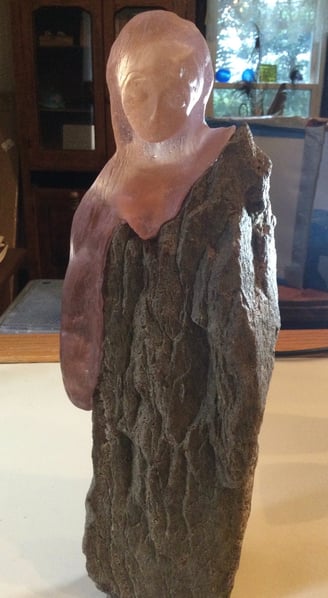
Cast Glass
The Casting Process
Each piece is first carved and created out of wax or clay. If clay is used, rubber is poured over the clay, the clay is removed, and wax is then poured into the rubber molds creating a positive wax piece.
Each wax piece is covered with multiple layers of plaster, silica and fiberglass. The piece is carefully cast and dried after which the wax is melted out of the mold.
The molds are then put into the kiln to dry at a low 200 degree temperature. This sometimes takes days depending on the size of the mold. Glass is carefully measured to ensure the mold fills precisely. Sometimes flower pots are used to hold the glass. As the glass melts, it flows from the bottom hole into the mold. The casting process goes through a number of stages with the top temperature holding at around 1500 degrees. The glass then needs to anneal or cure at around 900 degrees. This stage can last for many hours and sometimes days depending on the thickness of the glass. To keep the glass from cracking, the cooling process can be very long, especially for thicker pieces.
When the firing is complete and the pieces are completely cooled, the molds are carefully cracked open exposing the finished piece. Rough edges are ground and sanded and the piece is thoroughly cleaned.
While the Lost Wax Casting method is both difficult to execute and time consuming, the possibilities for creating different forms are endless. I am always struck by the beauty of the glass; the wide range of colors and the incredible way it changes with light.